#3 Operation
- What happens in the operational phase?
Don't worry, we'll take care of you.
A product or solution is considered to be in the operational phase when it has been completed from production and delivered to the customer for assembly and commissioning.
Each project will have a responsible project manager, and several different disciplines will be involved from design, through production to operation.
It is important with close follow-up of the customer to ensure the final delivery. It is usually much more demanding to rectify deficiencies after the installation is completed.
From concept to commisioning
For some projects, our presence will be needed to carry out assembly and commissioning, other times the customer takes care of this process with support from us.
The extent to which our service engineers are involved depends on the complexity and size of the project. Regardless of the size and complexity, we will of course always consider how the customer wants to carry out commissioning.
In the projects where our service engineers are present, they will assist with assembly and commissioning. Their main goal is to verify that the systems and components are installed and operate according to project- and client requirements.
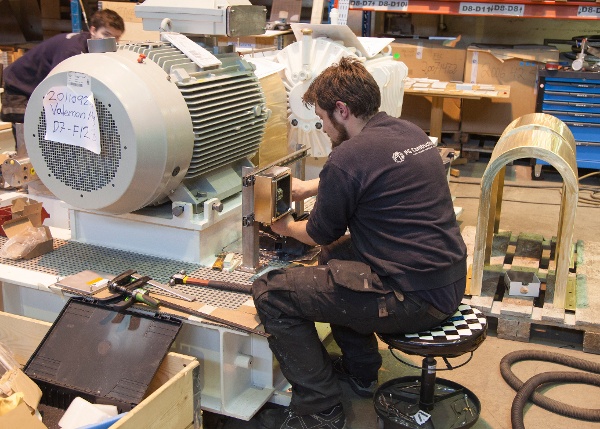
Necassery preperations
Our team will not be able to carry out assembly and commissioning until the customer has made the necessary preparations that are needed.
To ensure this process, we send out checklists where we require a signature and preferably photo documentation of each step.
Examples of challenges or issues we may encounter.
- Deficiencies with components or systems from third party suppliers
- Necessary preparations have not been carried out before installation.
- Predefined conditions that have not been implemented.
- The area where equipment is to be placed does not correspond to the stated dimensions
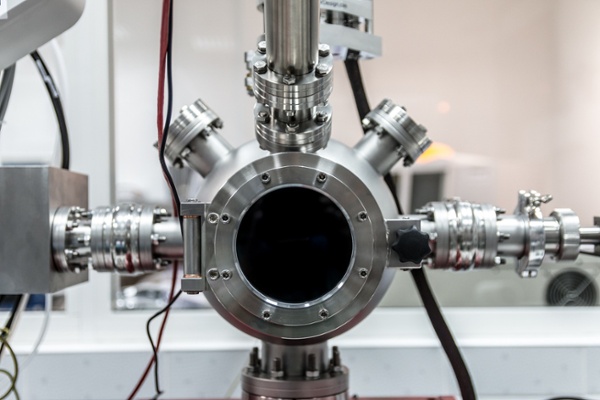
We'll take good care of you
Lifecycle Services Department
When the project is transferred from production and prepared for delivery, further follow-up of the project and customer is transferred to the Lifecycle services department (LCS).
LCS's main task is to ensure the entire life cycle of the products and to be a resource for the client. This may include commissioning, training, maintenance, modifications, upgrades, partial deliveries, support, repairs, and warranty handling.
Service Engineers
Service Engineers with global reach, ready to react at a moment’s notice.
Technical knowledge in a multidisciplinary field of mechanics, hydraulics and automation.
Extensive offshore and onshore experience with oil & gas, marine and industrial pump systems.
Our main task is to ensure the entire life cycle of the products and to be a resource for the client. This may include commissioning, training, maintenance, modifications, upgrades, partial deliveries, support, repairs, and warranty handling.
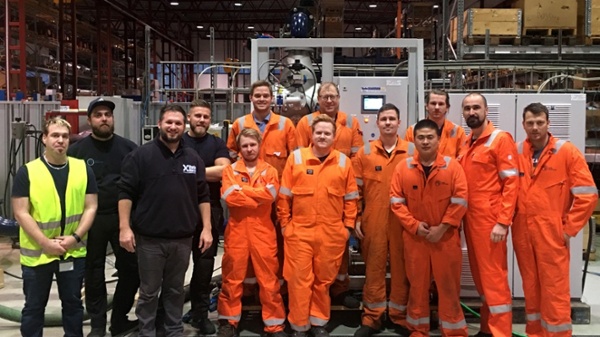
How to get started
Learn more about how we work. View the two previous steps "Design" and "Building".
#1 Design
Describe your challenge.
In cooperation with technical supervisors and the workshop, we will draw the first solution concepts in the form of descriptions, sketches or models to solve your challenge.
We proceed with GA drawings, which illustrates dimensions and functionality. Together we discuss, test and optimize.
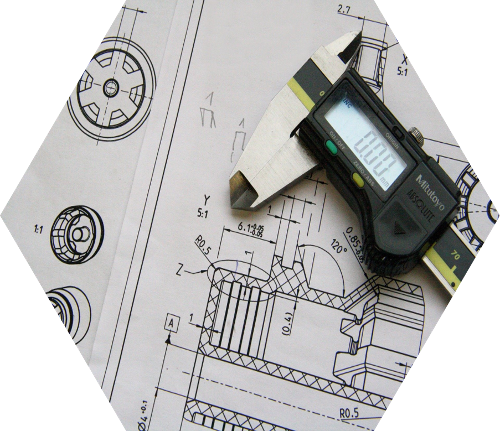
#2 Build
Now, let's build it!
We cut, bend, machine, weld, assemble, treat and test a variety of component in-house. From design we have detailed steel drawings that describes which parts we must process.
When all the steel parts have been made and welded together, we will normally carry out surface treatment with paint or acid pickling.
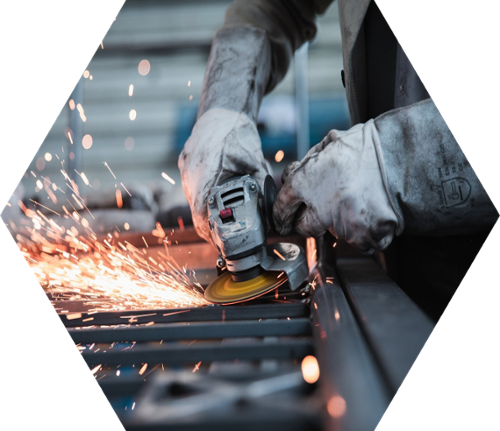